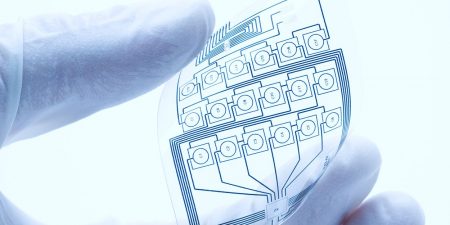
Credit: DuPont
Once a mere “science project”, printed electronics could soon become a commercial venture if chipmakers have their way.
As Semiconductor Engineering reports, the printing of electronics using conductive ink as opposed to lithography “is starting to move out of the research phase” and their “capability” has “captured the imagination of chipmakers on multiple continents and in multiple industry segments.”
“There are categories of things where printed electronics do very well,” said Dan Brewer, Executive Director at Brewer Science. “Anytime you need a flexible form factor that can be adjusted to fit a particular shape, this works great. It also allows an operation to benefit from lots of big data analysis because you can generate data from everywhere.”
While there has been talk of developing this kind of technology for more than a decade, the challenges have, up to now, hindered its progress.
“This has been on our agenda for the past 10 to 15 years,” said Janos Veres, Manager at PARC (formerly Xerox PARC, or Palo Alto Research Centre). “There are three things we envision. One is new form factors, including 2D devices. The second is integration of sensors, including optical and mechanical components. So instead of building these devices in tiny dimensions, you can spread them out. The third is on-demand, local, distributed manufacturing. So rather than building up inventory, you can guarantee to keep them fresh in the supply chain.”
There are a number of potential applications, both existing and new, for printed electronics, and the government of Denmark has already been embarking on a small-scale research program utilising printed sensors.
“If you think about a three-dimensional sensor today, you may have a humidity sensor or a temperature sensor,” said Gert Jorgensen, Vice President of Sales and Marketing at DELTA Microelectronics. “But with printed electronics you can have both of those and much more. So you can develop an ink where it could be applied to a protein or a non-organic film, and you can use that to sense things that are not detected today by a diode.”
“This could be used to determine food quality, too,” Jorgensen continued. “You can measure carbon monoxide, carbon dioxide, different chemicals and metals. You can glue this on a microcontroller and use it to detect bacteria. We take air samples today. This could be cheaper and faster. And today with diseases, you need to grow a culture in a lab. That could take a week. And there are still diseases you cannot see that way, such as influenza or bacteria that cause food poisoning. You may be able to detect that with ink. We’re at the research stage today. There are prototypes of inks, which are not being made yet in high volume, that can be made sensitive to light, bacteria, and even corrosion on screens in industrial applications. And if you can get inks to change colour, you can read them easily with image recognition technology.”
Industrial applications are also an “obvious” choice for this kind of technology.
“Today, you’ve got sensors that are basically glued together, and you’ve got miles of wires in a car,” said PARC’s Veres. “In automotive, they’re looking at integrating structures into a laminate to create new designs. So you may have panels overhead, and you can print 2D circuits and add a conformal piece onto or into those panels. It’s the same for wearables. You can have bio sensors that can sense more than 100 different biomarkers using foil-like structures.”
Sensors can also be put to good use in “warehouses and product packaging”, according to Veres, as well as in 3D printing. “3D printing did not take off as we had hoped,” said Stefanie Harvey, R&D program manager for flexible technology at SEMI. “But we are starting to see new materials being used here for things like antennas. What we’re also finding is that additive manufacturing doesn’t have to be a nozzle or ABS (acrylonitrile butadiene styrene, a thermoplastic polymer). You can have reproducibility and conformity and resistors at interesting geometries. There are lots of advancements being made.”
As well as the various benefits of printed electronics, however, they do also come with their own set of challenges and have to “undergo the same kind of rigorous verification, validation and testing as other chips.” The reliability of such sensors is “a key concern”, as is how long they will last, how easy they will be to replace, and how they will deteriorate over time.
“Durability is always a problem in printed electronics,” said Brewer. “In some ways, it’s more durable than silicon or metal and it’s very stable. But you do have to worry about the physical durability of a device, which could include everything from de-lamination to physical degradation like cracking when it is exposed to a harsh environment. You also have to figure out if heat is going to be a problem—do you need to create a heat-resistant flexible substrate—and does it need to be transparent.”
Nevertheless, with “momentum building” behind this particular area of technology, it seems likely that, once “the kinks are worked out”, the appeal and potential of printed electronics is set to be firmly on the rise.