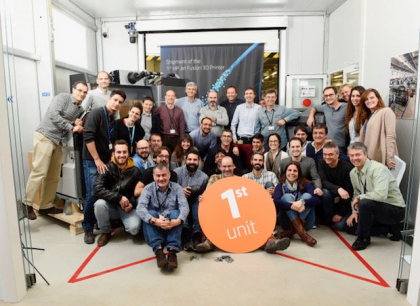
HP Inc’s 3D team celebrating shipping the first device
The OEM has been explaining how it has been using its 3D printing program to revitalise its own manufacturing processes.
As TCT explains, when HP first introduced its first 3D printing platforms, the purpose behind its Multi Jet Fusion technology was “to hand manufacturers a new tool.”
With HP itself being the kind of business it was trying to target with its 3D printing division, Stu Pann, the Head of Supply Chain, said, “Hey, go and see how many of those parts inside the 3D printer make sense to be 3D printed,” predicting that “maybe three or four of the parts would be economically viable for 3D printing.”
Instead, analysis found that 60 of the 112 plastic parts required for the printer “could, and should, be printed by a 3D printer”.
This discovery led to the launch of HP’s internal “Reinventing HP with Multi Het Fusion” initiative.
“We want to see this migrated into customer environments, but there’s no better place to start than home, and we have one of the biggest plastic supply chains in the world,” Scott Schiller, HP’s Global Head of Customer and Market Development, explained during Formnext 2018.
With various applications found for HP’s 3D printing in the company’s own production processes, the company’s Indigo division managed to reduce costs by 8o percent and reduce assembly by 91 percent, while the redesigning of the MJF air duct reduced cost by 30 percent and avoided $190 000 (€166,218) in capital expense.
The HP on HP program began by penetrating the products the OEM launched on the marketplace “and then it started to impact the way HP makes them.”
The application of MFJ was also beneficial when it came to bringing out a bigger version of the company’s Sprocket printer, which would ordinarily require “a separate SKU and production line.” Once design engineers had ensured “the tooling could change on the production line”, cost was reduced by 90 percent, “and average lead time was down from 13 weeks to two.”
“The obvious becomes possible because you have a way to action it,” Pann articulated. “When you think about how you get stuff down the conveyor belt and how you grip it, you can generate grippers and size, any shape, for a robot hand to pick something up. If you think about the old way of doing it, we have to go to a robotics company, order a special arm, get it fit, sometimes it would take two or three weeks because it wasn’t in stock. Now we can just do it.”
Now, the HP on HP program “is touching all stages along the product lifecycle, from prototyping through bridge production through full production through spare parts and inventory.”
“All we did as senior leaders was encourage the dialogue and encourage the experimentation. And that was enough,” Pann said. “This is a company of engineers and they like doing creative things so [when] they knew that we were smiling and supportive, they would go do it on their own.”
“When I think about the tremendous progress we’ve made in a short amount of time, I’m incredibly optimistic about reinventing our own business with Multi Jet Fusion, as well as what it means for large enterprises around the world transforming theirs,” concluded Christoph Schell, President of 3D Printing and Digital Manufacturing, HP. “We challenged our engineers and designers to look at how Multi Jet Fusion could positively impact HP’s business. One year later, we see examples across our business helping realise millions of dollars in benefits: lowering costs, unlocking new design possibilities, reducing time to market, and slashing our C02 footprint.
“We are making strategic decisions to use 3D printing, not because we can, but because we should. It makes economic, product performance, and environmental sense. When you think about the impact of the programme in its earliest days, our use of Multi Jet Fusion illustrates how 3D printing technology does have the power to digitally transform large enterprises.”