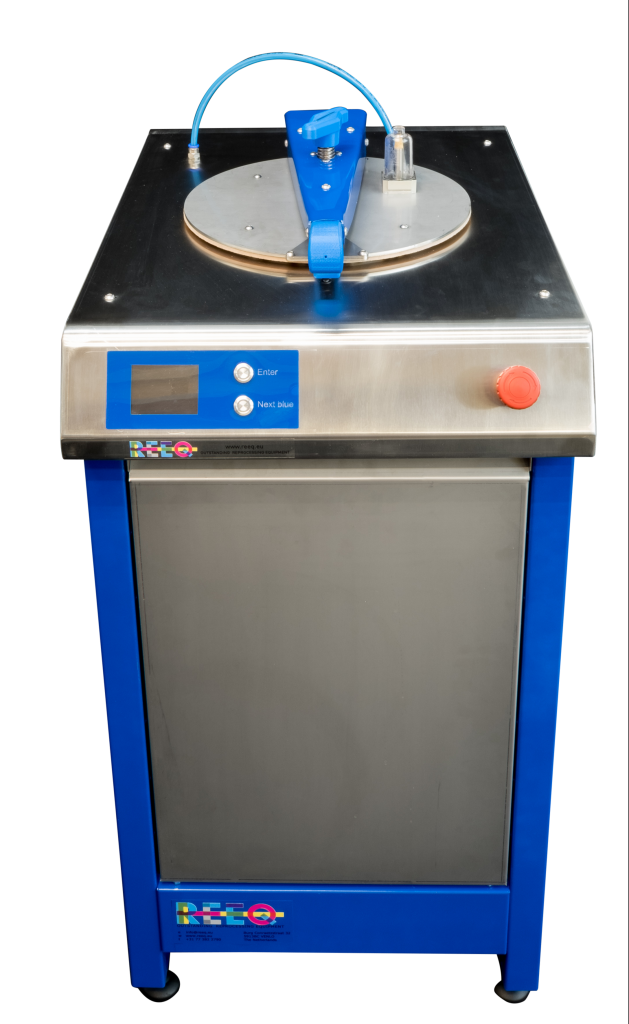
REEQ CC700 Cleaning Machine
One worker to process 100,000 cartridges a year was the challenge that led to the creation of REEQ entering the inkjet remanufacturing business in 2017.
Go back a few years and the challenge was given to Fons op het Roodt Industrial Design, a specialist industrial design company based in the Netherlands. The project proved to be very successful and more requests came for similar machines. Together with a select group of strategic partners, they founded REEQ BV in 2017.
Today REEQ produce a range of technology solutions for small and large companies engaged in the reprocessing of inkjet cartridges. The overriding focus is that the technology solutions are an integrated production process built around just 3 machines. These 3 machines enable one worker to process 100,000 cartridges a year, about 450 cartridges a day.
The process is fairly simple, but it is important that the operator is in control of the process to ensure the filling is efficient and avoids any mess.
Stage 1 utilises the REEQ CC700 cleaning machine to ensure that the cartridges are cleaned to remove all the residual ink, then the cartridges and print heads are rinsed before the centrifuge sins the cartridges dry.
The cleaning machine processes up to 72 cartridges per cleaning cycle and the average cleaning cycle lasts 45 minutes. The CC700 Cleaning machine is fully programmable to create the optimum cleaning cycle for your process.
Stage 2 utilises the REEQ CF700 cartridge filling machine is designed to work with virgin and non-virgin cartridges and easily and accurately fills a mix of cartridges ensuring no ink overflows.
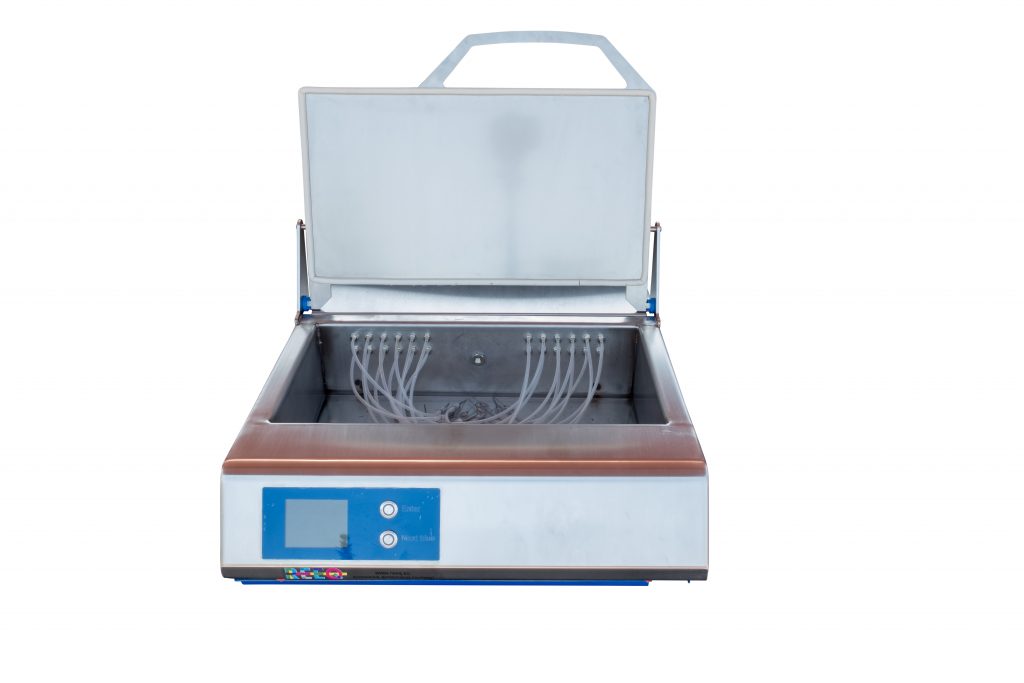
REEQ CF700 Filling Machine
CF700 Filling Machine
The CF700 is programmable to fill cartridges incrementally and to a pre-set fill level making the filling process easier, more accurate and less messy.
The filling process takes about five minutes, including loading and unloading, for XL inkjet cartridges (18ml – 20ml) and a little longer for larger cartridges. The batch size for standard cartridges is 24 black or 8 colour, but batches can be varied according to the size and type of cartridge being filled.
The Money Maker – The inkjet equivalent of the enlarged toner hopper is converting small cartridges into large ones. To do this you need to remove the cartridge cap and using the CM700 precision milling machine, mill out the inner walls, add a larger sponge and you have a larger capacity cartridge.
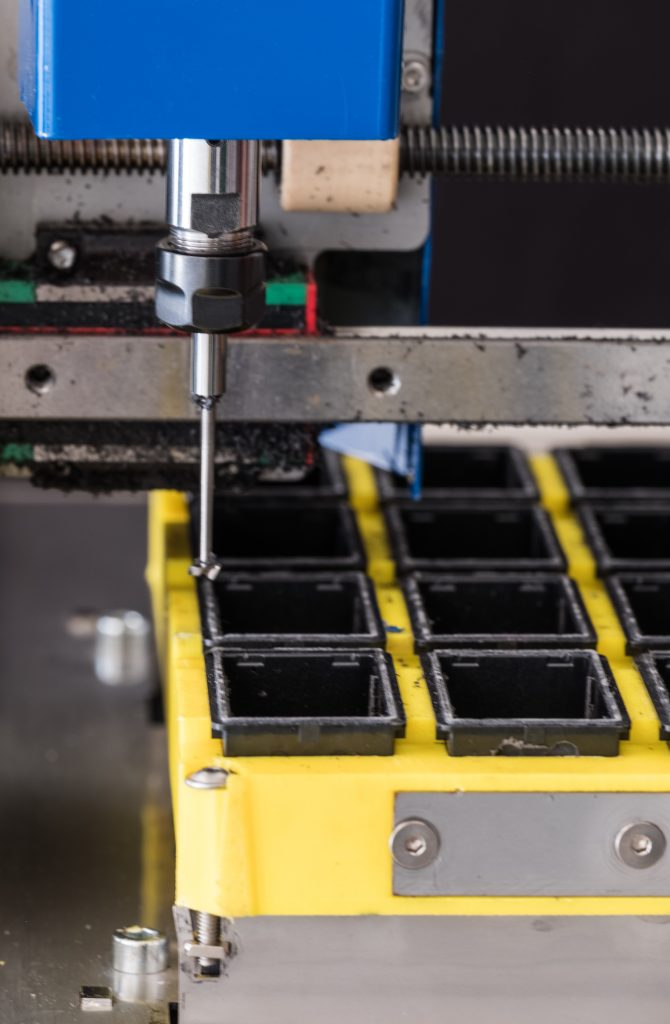
Precision cartridge milling
The REEQ CM700 precision milling machine has been specially developed for cartridge milling and pre-programmed to process inkjet cartridges. It can handle 24 cartridges per batch and has milling programmes for all cartridge types.
The capacities of the REEQ machines is a minimum of 100,000 cartridges per year and in many cases is significantly higher enabling capacity to build easily. For example, increasing production beyond 100,000 cartridges per year may only require a second operator.
The key feature of the suite of REEQ machines it that they are capable of processing the widest range of small, medium and large inkjet cartridges and tanks etc.
REEQ is a small company with highly skilled employees that deliver an adaptable approach to the development and production of their machines. The in-house engineering disciplines are electronics, mechatronics, mechanical engineering, software and hardware specialists as well as people who are working in the ink refilling industry for over 20 years.
The vision is to develop, design and build high-quality equipment for the ink cartridge refurbishing industry. The focus is creating a machine-based, integrated production process that enables just 1 operator to refurbish at least 100,000 cartridges per year in an efficient, quality-driven process that enables remanufacturers to boost their turnover and profit.
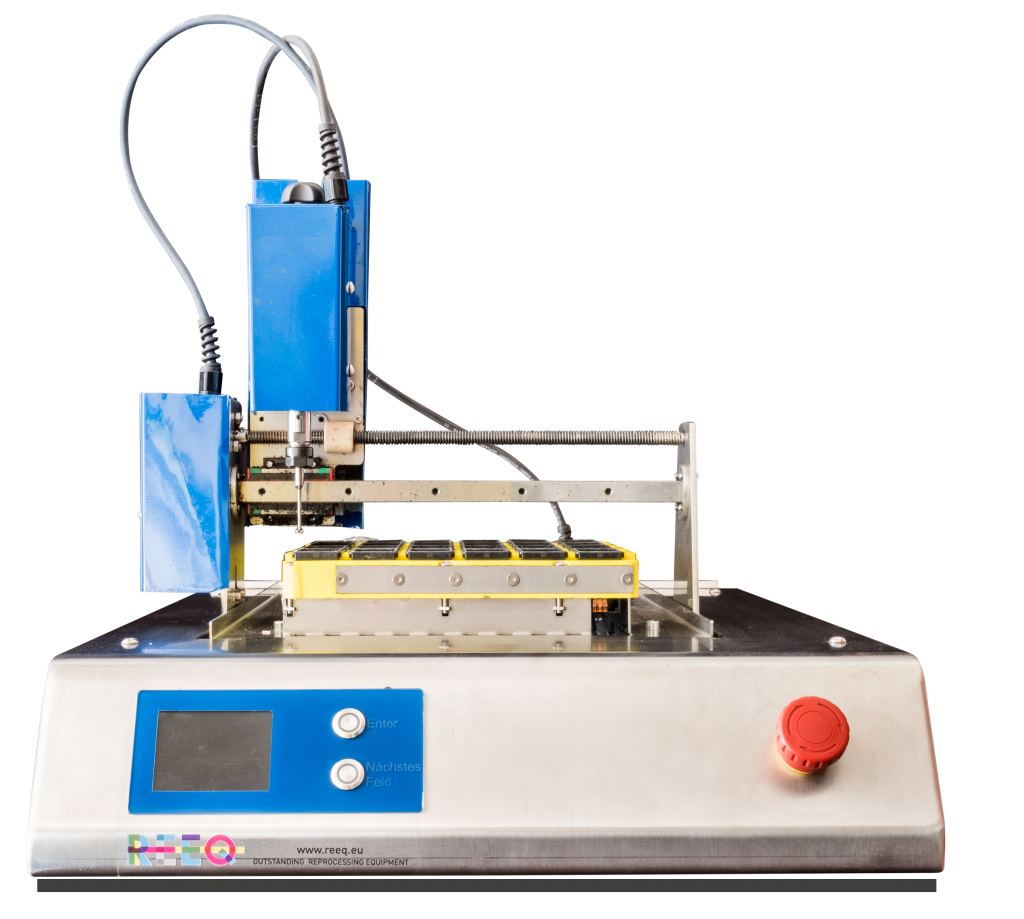
REEQ CM700 Cartridge Milling Machine
In June 2018 REEQ took on the inventory and support for the CBR range of machines for former CBR customers. The highly-rated CBR ShopTester units and modules and, while stocks last, CBR spare parts are available directly from REEQ.
In development is new test equipment as well as the development of special tools, fixtures and fittings to help improve customers inkjet refurbishing process. REEQ recently introduced a “pneumatic cap remover” the CRp is an example of a development item that is now available for everyone.
Just launched is the Ink Suction Unit, ideal for making those not quit 100% working cartridges, 100% working cartridges.
André Piels, REEQ’s CEO told The Recycler “We were rolled into the inkjet refurbishing industry 4 years ago as an Industrial Design & Engineering company. We are pleasantly surprised with the interest and use of our machines. We are currently completing one installation a month and are now exclusively focused on supporting the inkjet refurbishing market.”
The inkjet market is in transition with pockets of growth and decline, but refilling retains a significant market share. For remanufacturers, the challenge is to collect and process cartridges quickly and efficiently and to a consistent quality. The REEQ solution enables remanufacturers to deliver viable and profitable solutions that help, reduce the environmental crisis.
Apart from the cost of the empty, labour is a significant factor and manual refilling can be both cost-prohibitive and inconsistent. The REEQ machine-based, integrated production process enables 1 operator to refurbish at least 100,000 cartridges per year in an efficient, cost-effective, quality-driven process that enables remanufacturers to boost their turnover and profit.
Burg Conraetzstraat 32
5913BC VENLO
The Netherlands
e info@reeq.eu
w www.reeq.eu
P: +31 475 537 353 – Enquiries
P: +31 77 382 2790 – Technical Department